FEATURES
Ongoing Research Topics
"Throughout the years, KOBELCO has proactively engaged in efforts to seamlessly integrate individual solutions into their manufacturing sites. No matter how far technology advances, it is always vital to assess how useful such technologies are in tackling the issues and solving problems faced at the site of manufacture. From this perspective, we aim to conduct research on numerous topics that combine our knowledge with Osaka University's expertise in the field of AI solutions."
Cutting Process Support System Project
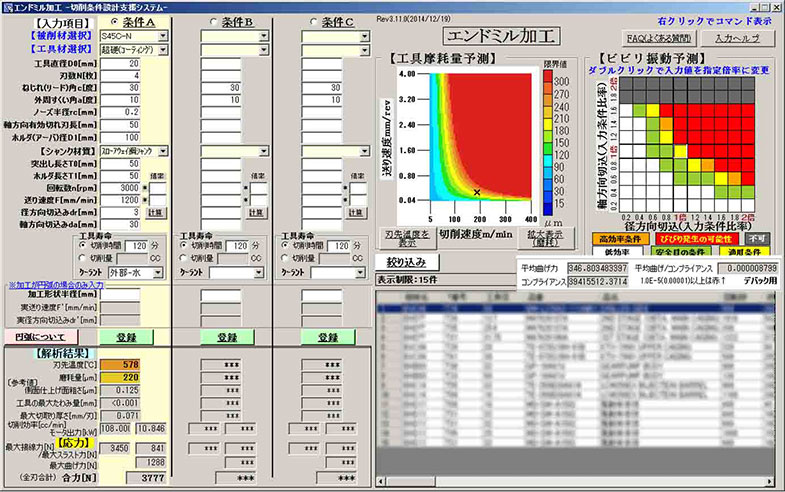
Project Concept
Through this project, we aim to support manufacturing innovation in the machining industry by proposing various "cutting process solutions" that can contribute in such areas as the enhancement of machining efficiency, avoidance of manufacturing problems, reduction of costs, and optimization of cutting processes. The concept for this project focuses on the realization of "machining support services" that can be used to propose measures to enhance performance in a way that matches the specific needs of each manufacturing site based on results obtained through performing data analysis and simulation in a manner that combines AI technologies with data collected from various machining processes.
Research Overview
Our "machining support services" involve research being performed with the aim of optimizing machining process design and cutting conditions through the utilization of various forms of data (cutting resistance, cutting temperature, etc.) that is obtained through process monitoring and the utilization of AI technologies.
- Tool wear prediction technologies:
- These technologies calculate the degree of tool wear by identifying "cutting edge temperatures" through cutting simulations and by performing experiments to obtain the "reactive tendencies of the tool to workpiece contact area."
- Chattering vibration predictive technologies:
- The regenerative effect that generates self-excited vibrations is caused by fluctuations in the amount of cutting performed that results from phase differences in the vibration trajectory of the cutting edge. These technologies are used to suppress chattering vibration by controlling these phase differences.
Project Phases and Current Progress
By conducting interviews with manufacturing companies in the machining industry (mainly in the field of cutting processing), we will organize and analyze data to identify a wide range of issues related to cutting processes.
Phase1
Engaging in dialogue with companies
Identifying the core of their problems
Phase2
Co-creating ideas to lead us into the future
Phase3
"Conducting technological assessments Co-creating solutions"
Current
phase
Phase4
Conducting pilot projects together with companies
Phase5
Achieving enhanced and enriched manufacturing through societal implementation
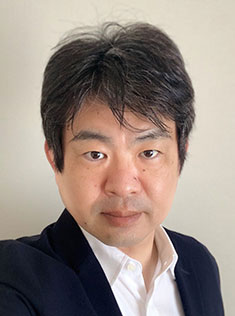
Lead Researcher
Cutting Process Project Leader
Materials Research Laboratory
General Manager
AKAZAWA Koichi
Researcher Comments
By maximizing the potential of combining cutting process technologies with AI technologies, our diverse group of project members will work in unison to enable us to realize the future of manufacturing.
Contact us to inquire about this project
Contact formPress Forming Support System Project
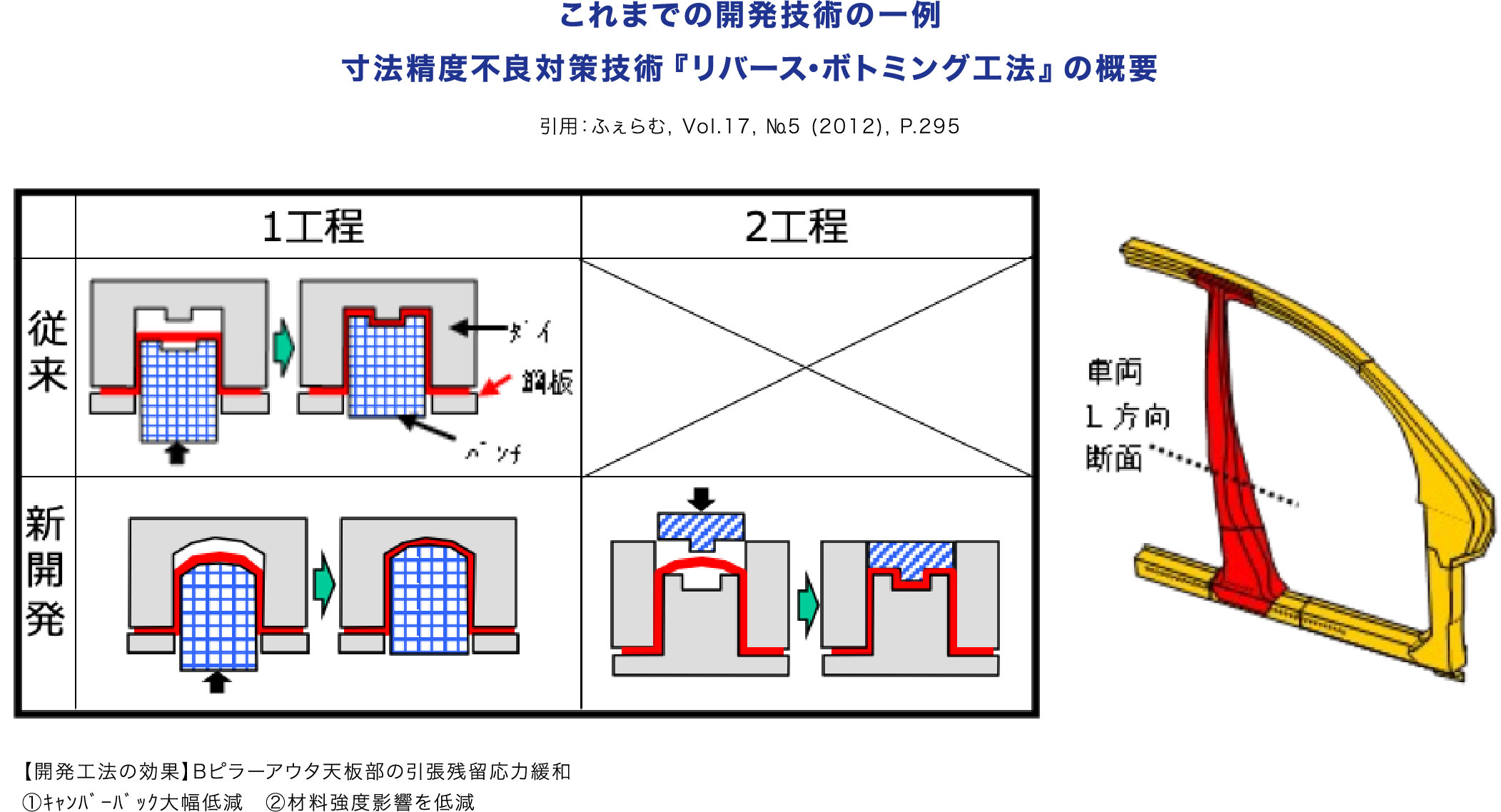
Project concept
Through this project, we aim to support the implementation of various technologies and the transferring of highly-sophisticated skills to solve issues related to press forming by offering solutions that can enable companies to achieve advanced press forming simulations and to collect and analyze related information. After engaging in sustained dialogue with the individuals involved at our customers' manufacturing sites to have them share information on the specific problems they are facing, we then combine the wealth of manufacturing technologies we have accumulated with the latest AI technologies to find a solution. Furthermore, we dive even deeper by examining individual issues being faced on an industry-wide and business management level in order to develop products and technologies that can contribute to the advancement of the industry as a whole with the aim of improving long-term business competitiveness in the global market.
Research Overview
We are currently engaged in evaluating the feasibility of a variety of technologies as we focus on gaining an understanding on the issues our customers are facing. We are not content to stop at the press forming simulation technologies and process technologies that we have developed in the past, and we intend on boldly embracing new technologies to enable us to move forward in the research and development of further elemental technologies as we aim to establish a comprehensive technological platform for manufacturing.
Project Phases and Current Progress
Phase1
Engaging in dialogue with companies
Identifying the core of their problems
Phase2
Co-creating ideas to lead us into the future
Current
phase
Phase3
"Conducting technological assessments Co-creating solutions"
Phase4
Conducting pilot projects together with companies
Phase5
Achieving enhanced and enriched manufacturing through societal implementation
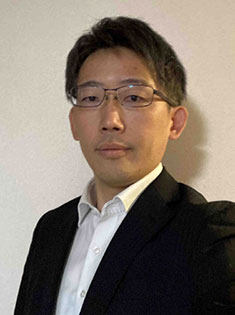
Lead Researcher
Press Forming Project Leader
Application Technology Center
Structural Design Research Section
Senior Researcher
IHARA Ryohei
Researcher Comments
Although this is an arduous endeavor into a realm that is unknown, we will take on the challenge by assembling the collective wisdom of our project members as we take each step and steadily move forward.
Contact us to inquire about this project
Contact formKOBELCO Future Pioneering Co-Creation Research Center Library of "Technological Seeds"
"Here you can find a portion of the technological know-how that has been accumulated at KOBELCO to resolve real-world issues being faced at the site of manufacture.
We are currently in the process of identifying project themes for each of these potential ""seeds of research,"" by further combining them with Osaka University's knowledge on AI solutions.
In addition to what is shown here, we possess numerous technologies and systems that can meet your company's needs.
Furthermore, there are also many efforts our researchers are engaged in, which we are not at the liberty to disclose as of this moment. If you are interested, please feel free to inquire further."
Product Development and Design
- Visualization and predictive technologies for heat and flow inside machines
- Predictive and control technologies for noise and vibration
- Metal surface control technologies
- Dissimilar & Similar Joining Process
- Fill Vehicle CAE solution
- Technologies to increase added value for machine products through the utilization of image recognition AI
- Simulation technologies that use computational science
- Enhancing efficiency and sophistication of material design through the utilization of AI
Manufacturing Process Design
Production Control, Quality Control, and Automation
- Production Scheduling and Logistics System for Machinery Plant of the make-to-order
- Optimal Production Control for High-mix Variable-volume Factory
- Diagnostic/Predictive maintenance technology for machinery
- Fault prediction and diagnostic technologies for processes
- Shape measurement technologies, high-temperature measurement technologies
- Image-based quality inspection technologies, non-destructive inspection technologies
- Control technologies for automation and the enhancement of yield
- Disturbance suppression technologies to reduce environmental impact through the utilization of AI
Human Resource Development and Skills Transferring
- Technologies to establish ICT platforms to foster the growth of service technicians
- Operator support technologies based on the accumulation and utilization of skilled, experiential knowledge
- Operator support technologies based on the visualization of production processes
- Technologies to support the optimized design of manufacturing conditions through the utilization of databases
- Technologies to support the planning and design of production sequences through the utilization of performance data
- Quantification technologies for visual and sensory inspections based on AI
- Off-line automatic teaching systems for welding robots